Dry Lamination vs Solventless Lamination
In the flexible package industry, the composite material combines the advantages of different layers, as better barrier for products inside.
Such as our material Alu-Alu or Alu/PE or polylaminate for wine capsule, they are composited materials with more than two layers. It’s one key character is peel-off strength between two layers, during the packaging production, the de-lamination is a big problem of quality, to avoid such problem, we should use the right lamination machine & lacquer.
Now in China market of flexible packages, there are mainly two types of lamination machines: dry one & solventless one, its configuration, cost, process, etc. are similar, but also different, please take this table for reference.
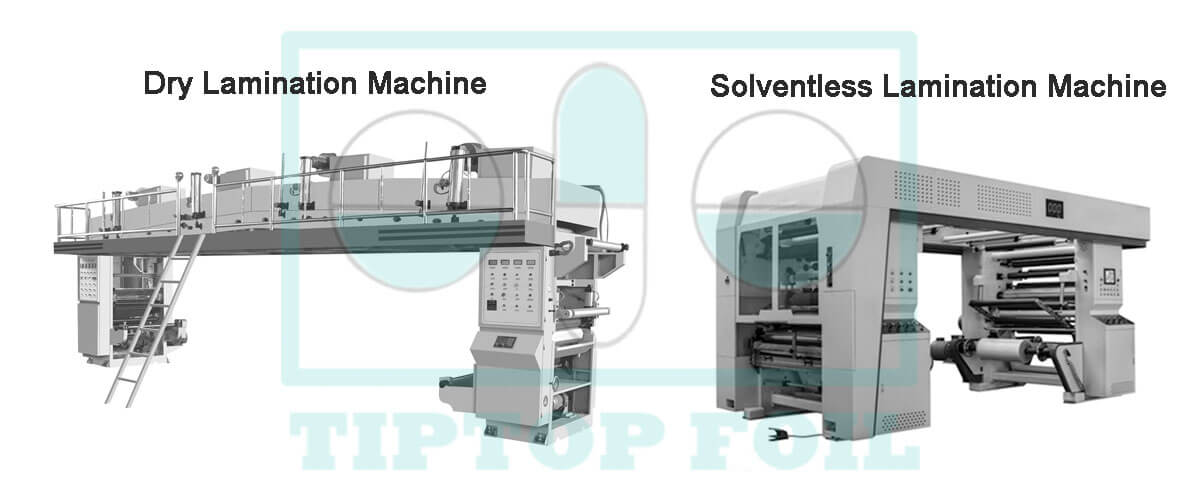
dry lamination vs solventless lamination
Item | Dry Laminating Machine | Solventless Laminating Machine |
Configuration & layout | Long, to add the heating & cooling channel to dry the lacquer | Short, only winding, coating, rewinding rollers |
Energy consumption | High, since more electricity or gas for heating & cooling | Low, electricity only for winding & rewinding |
Machine price | High | Middle |
Production cost | High, since solvent & special stock area needed, and more energy for heating & cooling | Middle |
Lamination speed | Low, normally 50-150m/min | High, normally 200-300m/min |
Coating | Stop to change the roller with different mesh to adjust the quantity per m2, low efficiency | Online change the speed of plain rollers to adjust the quantity per m2, high efficiency |
Drying | Key process to control quality | None |
Curing | Auxiliary process to control quality | Key process to control quality |
Peel-off strength | High | Middle |
Note:
- in general, the solventless lamination is better and eco-friendly in the area of production & cost, but for some usage, like cold forming with big punching pressure, as bag with heavy content or for boiling, etc. the dry lamination will be available recently.
- Now for the solventless lamination between aluminum and another film, its peel-off strength is not still good enough yet.
As for Alu-Alu in Tiptop, the lacquer between BoPA and Alu & Alu and PVC that we are using is from USA, plus our modern dry lamination machine and developed curing process, which ensure good performance during the packaging production, such as no delamination and cracking.